Quality
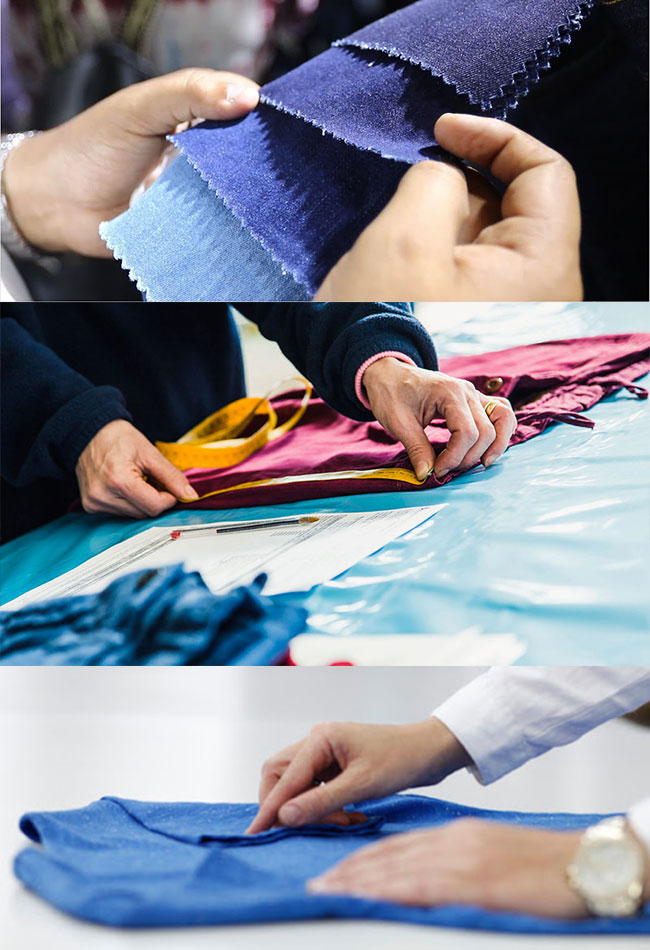
The process of delivering a quality product to our customers is divided into two key areas.
1) Prevention
The prevention part is taken care of by our Quality Assurance (QA) team which, under guidance from customers, set the standards for quality and supervises all elements of pre-production work Such as the fitting and styling details. The prevention part is also supported by in-house testing labs which make sure that the required testing procedures are undertaken before the production process starts.
2) Control
The control part is taken care of by our Quality Control (QC) team, which ensures the product standards set by the customers in co-operation with our QC team are implemented throughout The production process, and that the final products are as per our customer’s specifications. QC service takes place before the bulk fabric is cut. It consists of the elements listed below.
• Reporting of fabrics & necessary accessories arrival status.
• Visual control of fabrics: weight/m2, color, hand feel etc.
• Forecast of production timing (starting date, assigned capacity, daily output and finish date).
• Checking with production supervisors whether they think the style is feasible in conformity with the approved samples.
Category of Inspection
Usually, Our QC carry out their inspection in four stages in accordance to the MIL-STD-105E along with AATC, ASTM and ISO codes & standards. The level of inspections are used for the 4 pre-shipment inspections are as follows:
1. Pre-Production Check (PPC)
2. Initial Production Check (IPC) –Single Sampling Plan General Level I
3. During Production Check (DUPRO)–Single Sampling Plan General Level I
4. Final Random Inspection (FRI) – Single Sampling Plan General Level II